PCB Rework & Repair Services
Precision component removal, replacement, & soldering with PDR infrared technology
Reliably extend the life of PCBs & ensure optimal performance
PCB rework and repair services are vital parts of the manufacturing and maintenance process. During these steps, defective or damaged printed circuit boards can be restored to full functionality without the need for costly replacements.
Our certified production team at ETEMCO uses state-of-the-art infrared rework equipment, as well as a full arsenal of hot air, and precision soldering tools to complete advanced rework when required.
Save costs by salvaging & repairing
Both rework and repair help cut costs by avoiding the need to scrap or completely remake the PCB. It’s especially valuable for prototyping, product development, and hard-to-replace boards. By partnering with us to repair existing boards, your business will reduce waste, save costs, and minimize production delays.
Replace components with no damage
Our skilled technicians replace PCB components with precision and extreme care, leaving behind no damage to surrounding parts. We use advanced tools and controlled techniques to maintain the integrity of the PCB throughout the process.
Correct defects and soldering issues
Using industry-standard techniques and inspection tools, you can rely on us to identify and fix problems efficiently, such as misaligned components and cold solder joints. This enables long-term reliability and reduces the likelihood of future failures in the field.
PDR infrared rework — the core of our PCB repair
Non-contact, precision heating for safe & reliable rework
Our PDR IR-E3M rework station is the gold standard for BGA/SMT component rework and replacement. With advanced technology, such as focused IR component heating, 3-zone board preheat and a split beam prism viewing system, rework has never been easier, more reliable, and more accurate.
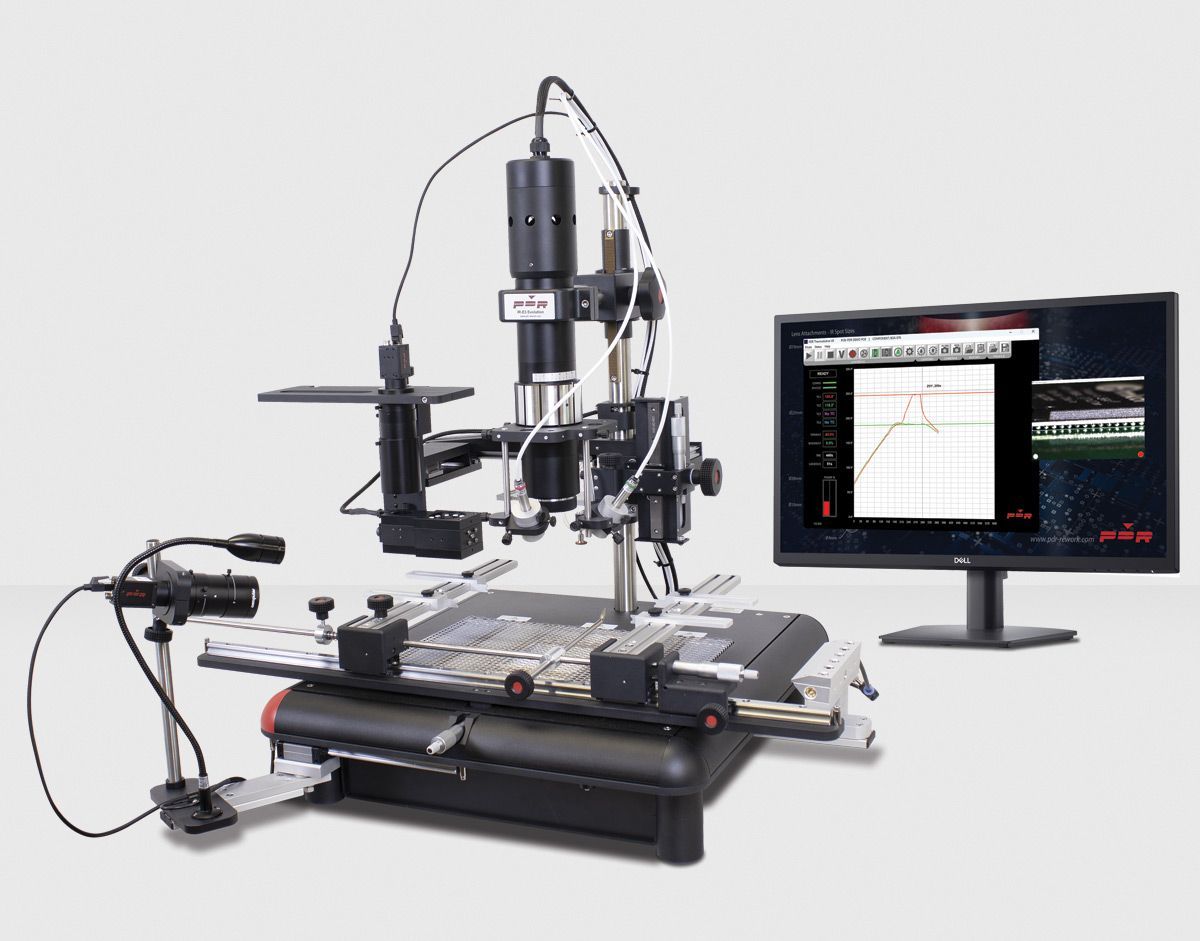
Precision Heating with No Airflow Disruption
As part of PDR’s infrared technology, uniform heat is delivered exactly where it’s needed without the disturbance that traditional hot-air systems cause.
Minimizes Thermal Stress on Nearby Components
The PDR's advanced focusing capability allows our technicians to direct the heat exactly where it needs go, while nearby components remain undisturbed. This ensures that the rework is done skillfully and accurately, while maintaining superior quality.
Optimized for BGA, QFN & Fine-Pitch Devices
The PDR Infared rework system is specifically designed for reworking bottom-terminated devices as well as fine-pitch SMT components.
Works Across Various PCB Materials & Designs
Highly versatile, PDR infrared rework is ideal for a wide range of PCB designs. It's suitable for standard board designs, aluminum clad boards, as well as multi-layer boards with heavy copper pours.
BGA Rework
During a ball grid array (BGA) rework, we adhere to the following steps:
- Diagnosis
- Site cleaning
- Component removal
- Placement of new component
- Reflow soldering
- Inspection
QFN Rework
As part of the quad flat no-lead (QFN) rework process, we go by the steps below:
- Site cleaning
- Component removal
- Solder paste application
- Placement
- Reflow
- Inspection
Bottom Terminated Devices Rework (BGA's, QFN's, etc.):
- Fine Pitch Rework
- Standard SMT Rework
- Through-hole Rework
When should a PCB be replaced instead of reworked??
A Printed Circuit Board (PCB) should be reworked rather than replaced when addressing minor manufacturing defects, component failures, or design modifications, and when the cost of rework is less than the cost of replacement. Rework can also be used to improve product quality and reduce waste. Conversely, PCBs should be replaced when the damage is severe, the rework is too complex, or the cost of rework is too high.
How does PDR infrared rework compare to hot air or convection rework?
IR rework offers advantages over traditional hot air or convection rework by providing a more precise and controlled heating process. PDR IR systems use focused IR beams to heat specific components, minimizing heat transfer to surrounding areas. This precision allows for more accurate temperature profiles, which is crucial for rework operations, especially with sensitive or densely packed PCBs.
What defects can be repaired through PCB rework?
PCB rework can repair a wide range of defects, including component failures, broken traces, solder bridges, cold joints, and physical damage. It also allows for modifications, upgrades, and design changes. The vast majority of component level defects can be reliably reworked by a trained technician.
How does X-ray inspection help ensure quality in BGA & QFN rework?
After reworking or replacing a BGA, QFN, or other bottom terminated device, it is critical to inspect the resulting rework to confirm the quality of the workmanship. Since the majority of bottom terminated connections can not be visually inspected since they are obscured by the device, the use of X-ray is our preferred inspection method.
Common questions about PCB rework & repair
Get exceptional PCB rework & repair services
Fast quotes, responsive services, & scalable rework
At ETEMCO, we help you bring your product to market faster with our high-quality, compliant PCB rework and repair services. Our team brings years of experience to each project, providing reliable, precise, and high-performing solutions.
Reach out today and learn more about our services and how we can assist with your project.